Introduction
Food processing facilities are continually looking for ways to increase their production capacity – many times by increasing shifts or increasing the amount of production lines. But an often overlooked opportunity to provide more production time is to reduce the time spent cleaning.
When it comes time to shut down food processing and switch over to clean and sanitize facility food production areas, there are a variety of ways to get the job done. Many surfaces within the facility need to be cleaned using washdown equipment through manual rinsing / foaming / sanitizing with a combination of spray guns, foam wands, sanitation sinks, etc.
In addition, many of the critical product contact parts in the production line are also Cleaned-Out-of-Place (COP’d). These parts can include weigh scale parts, elevator buckets, trays, buckets, barrels, fittings, hoses, and much more. The method to clean these parts is varied and can often be similar to cleaning surfaces where more manual methods are employed. The problem with these processes are that they can be very labor, utility, and time intensive.
The Traditional Way
To help improve the cleaning process – reduce time to clean, reduce utilities, and reduce labor – many food manufacturers turn to COP Parts Washers. These systems are typically manually operated to semi-automated and help to improve certain aspects of the cleaning process.
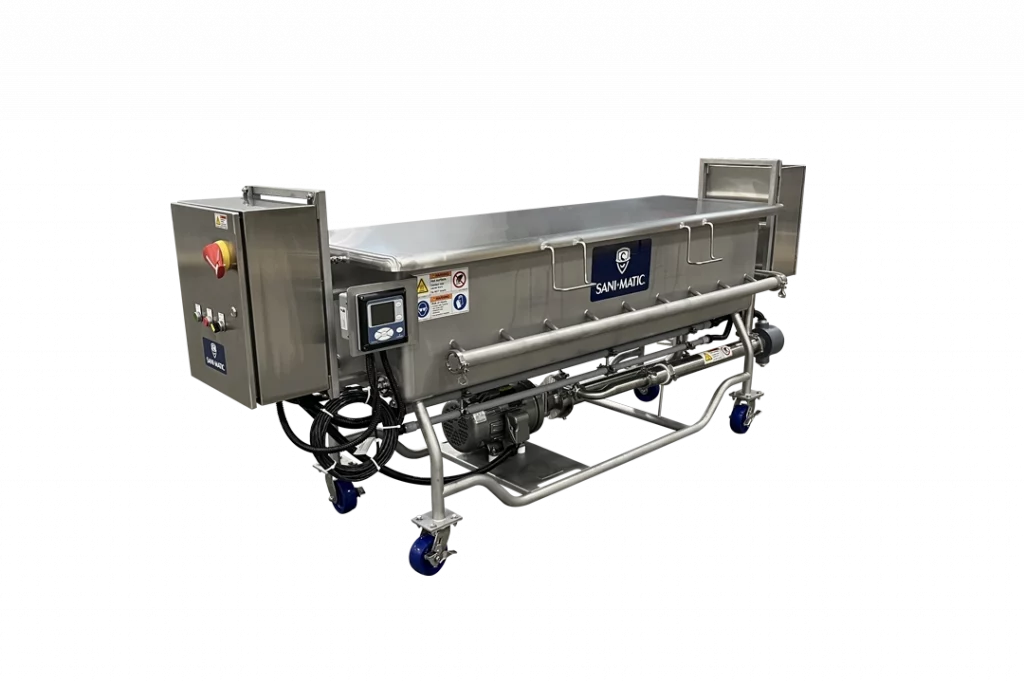
Many facilities use the COP Parts Washer primarily for the chemical wash step of the cleaning process. The COP Parts Washer is filled with water, chemical is added , and the water is heated to the cleaning temperature. The operator takes the part out of the process, rinses off heavy soils, and uses the COP Parts Washer for the chemical wash to break down the heavy soils. The part is removed and rinsed to remove chemical, and then sanitized before being put back into the process for the next run.
7 Touch Points of COP Parts Washers
While the chemical wash automation provided by the COP Parts Washer certainly does improve efficiencies when compared to manually cleaning, there are still many touch points from an operator standpoint and a fairly significant amount of time is still spent handling the parts – which takes time, increases risk of part damage or lost parts.
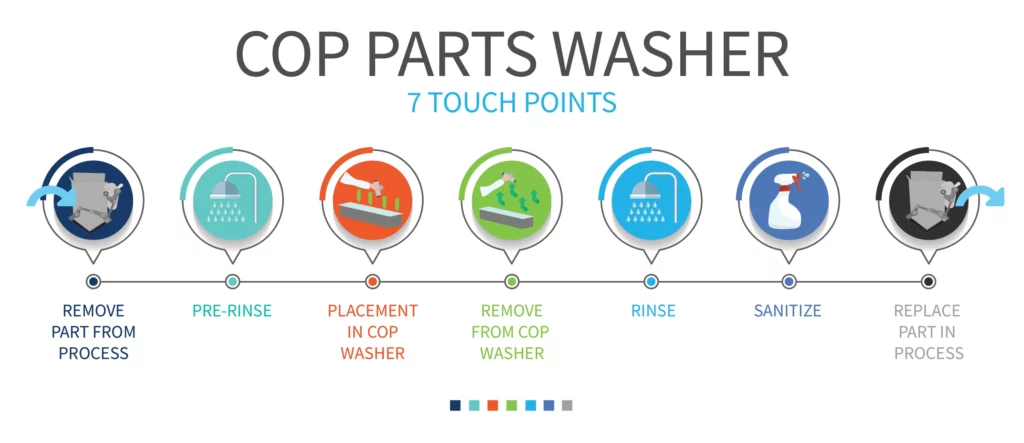
Think about the scenario described above – if you stop and count the touch points that the operator has with the parts, it Is roughly 7 times that the operator interacts with the part (remove from process; pre-rinse; place into COP Parts Washer; remove from COP Parts Washer; Rinse; Sanitize; replace back into process).
How can we reduce this time spent cleaning? And can we make it use even less utilities, be more repeatable, be easily recordable, and be consistent every single time?
The New Kid on the Block
As a reader, you may be familiar with Clean-In- Place (CIP) Systems as a way to automate cleaning of processes that can be cleaned without disassembly (in place) such as process tanks and process lines. These systems are often fully automated with Programmable Logic Controllers (PLCs) that control the sequencing and parameters, operated via Human Machine Interfaces (HMIs).
Enter the Cabinet Washer – the fully automated “CIP” equivalent for cleaning out of place. Parts are still taken out of place from the process, but are then placed into a Cabinet Washer to be cleaned (for a larger part like a large vat washed within a Vat Washer) or for numerous smaller parts often racks are utilized to hold the parts in place while being cleaned within the Cabinet Washer.
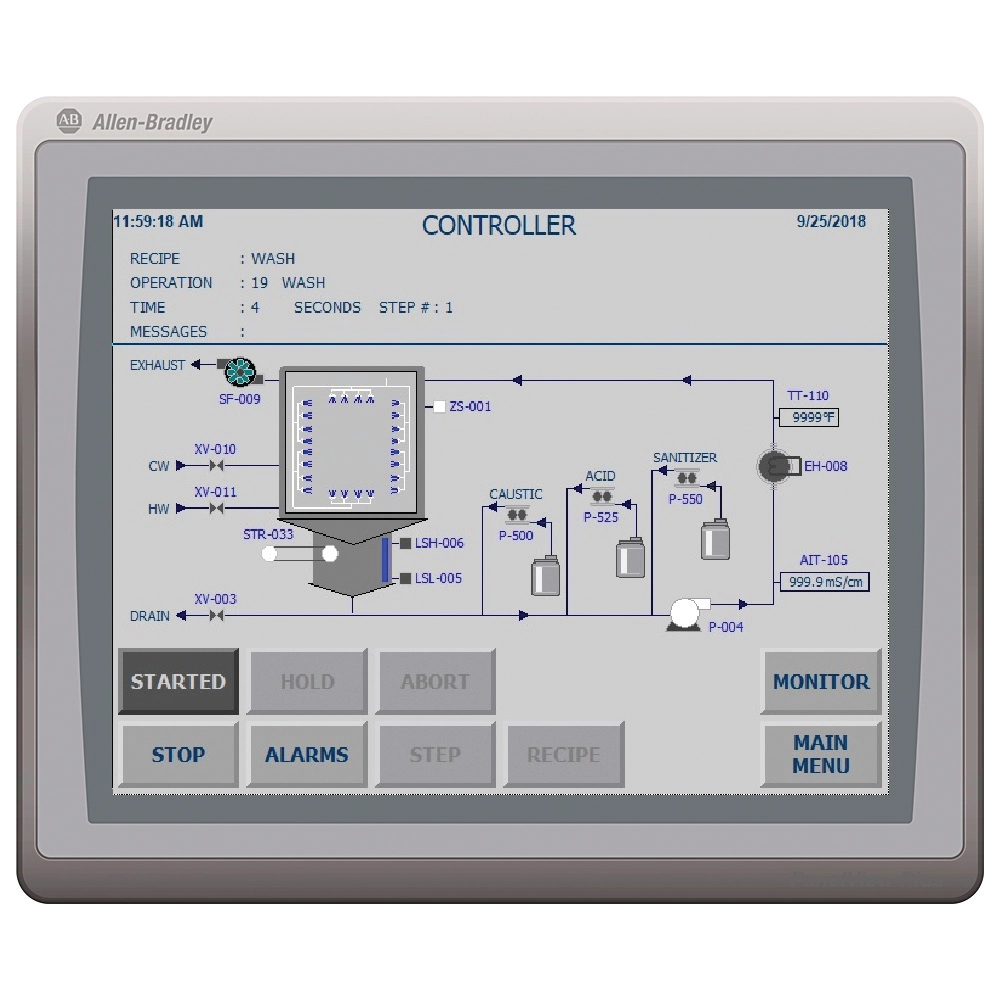
The advantages of these automated, hands-off systems are numerous – reducing time to clean, reducing labor, reducing utility use, improving consistency of cleaning, reducing part damage or loss, improving operator safety, and allowing for better data recording – let’s take a closer look at each of these areas.
Reducing Time to Clean
Remember the COP Parts Washer touch points? 7 total times the operator interacted with the part – that means that a lot of time is just spent in transferring and handling the part, let alone the actual cleaning. And again, while the COP Parts Washer did the chemical cleaning phase of the job more efficiently, manually rinsing or sanitizing parts takes a lot of time.
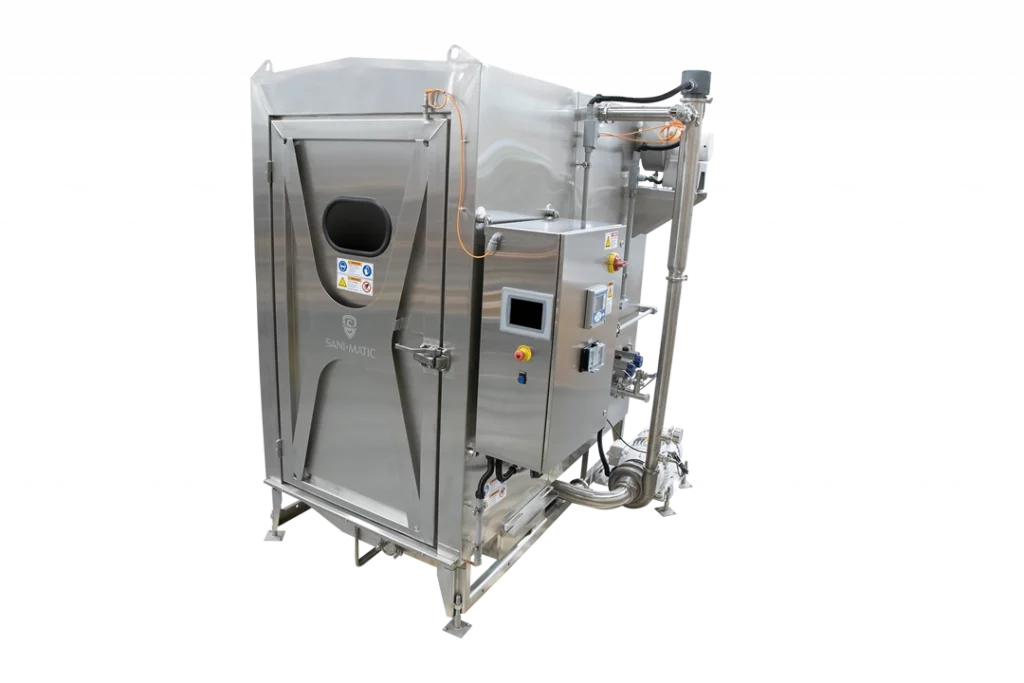
The Cabinet Washer does all the cleaning steps – pre-rinses, chemical washes (multiple, if needed), post-rinses, sanitizing (and even drying – if needed) – automatically and efficiently. In the case of a Cabinet Washer that uses racks to load the parts, all that is needed from the operator is to load the rack, push it into the Cabinet Washer, and hit start. The operator comes back once the cycle is completed and unloads the clean parts back into the process. A batch of process parts that perhaps took 2 hours to clean now takes less than 30 minutes.
Reducing Labor
Reduced time to clean inherently reduces the labor hours needed to clean. The beauty of the Cabinet
Washer is that the cleaning cycle occurs automatically so that operators can be either be getting the next
batch of parts ready for cleaning or be reassigned to other cleaning or production tasks while the cleaning happens automatically.
Reducing Utility Use
Most manual cleaning processes or the COP Parts Washer process described here includes rinsing with spray guns or foaming with chemical wands. These processes can consume a significant amount of heated water and chemical which can quickly add up over the course of a cleaning shift – think thousands to tens of thousands of gallons per cleaning operation. Cabinet washers can often use much less water (and inherently much less heating utility and chemical) since they are contained and often recirculated. A
pre-rinse, chemical wash, post-rinse, and sanitize for a large rack full of parts could use less than 100 gallons of water – an impossible feat when trying to manually clean the same quantity of parts.
Improving Consistency of Cleaning
Both the manual cleaning and COP Parts Washer cleaning have significant variability in how the part is cleaned. Did the operator not turn the part as to expose a critical section of product contact surface when sanitizing? Did they not check to make sure the COP Parts Washer temperature was sufficiently hot? Is the chemical concentration of the COP Parts Washer per the plant Standard Operating Procedure (SOP) requirements?
Even with the proper training, these and other variables are often very hard to control – we are all human! The Cabinet Washer takes this variability out of the equation with its automated controls system. The cleaning variables of TACT (Time, Action, Chemical, and Temperature) are all controlled and monitored so that if you verify cleaning under certain conditions for your process parts, they will be cleaned time and time again. In addition, customized racks hold the process parts in an orientation that exposes the critical
surfaces that need to be cleaned to the Cabinet Washer’s sprays of water and cleaning solution.
Finally, if your processes changes in the future (as it typically does!), automated Cabinet Washers can have adapt with various parameter adjustment – cycle times, temperatures, steps ran, chemical concentrations, etc. – changed to meet your new process parameters with different cleaning cycle recipes.
Reducing Part Damage or Loss
Back to the 7 touch points of the operator – the more that a part is manually handled, the higher the chance of lost or damaged parts. Scratches and dents not only look bad on your process parts, but they can then create harborage areas for bacteria that are harder to clean. In addition, many process parts such as weigh scale buckets cannot be damaged if they are to function as intended.
Cabinet Washers with racks that are customized to hold specific process parts contain and keep safe these items during transportation from the process to the cleaning room or area. You can think of these racks as customized organizational holders for your parts – they ensure no part
is left behind!
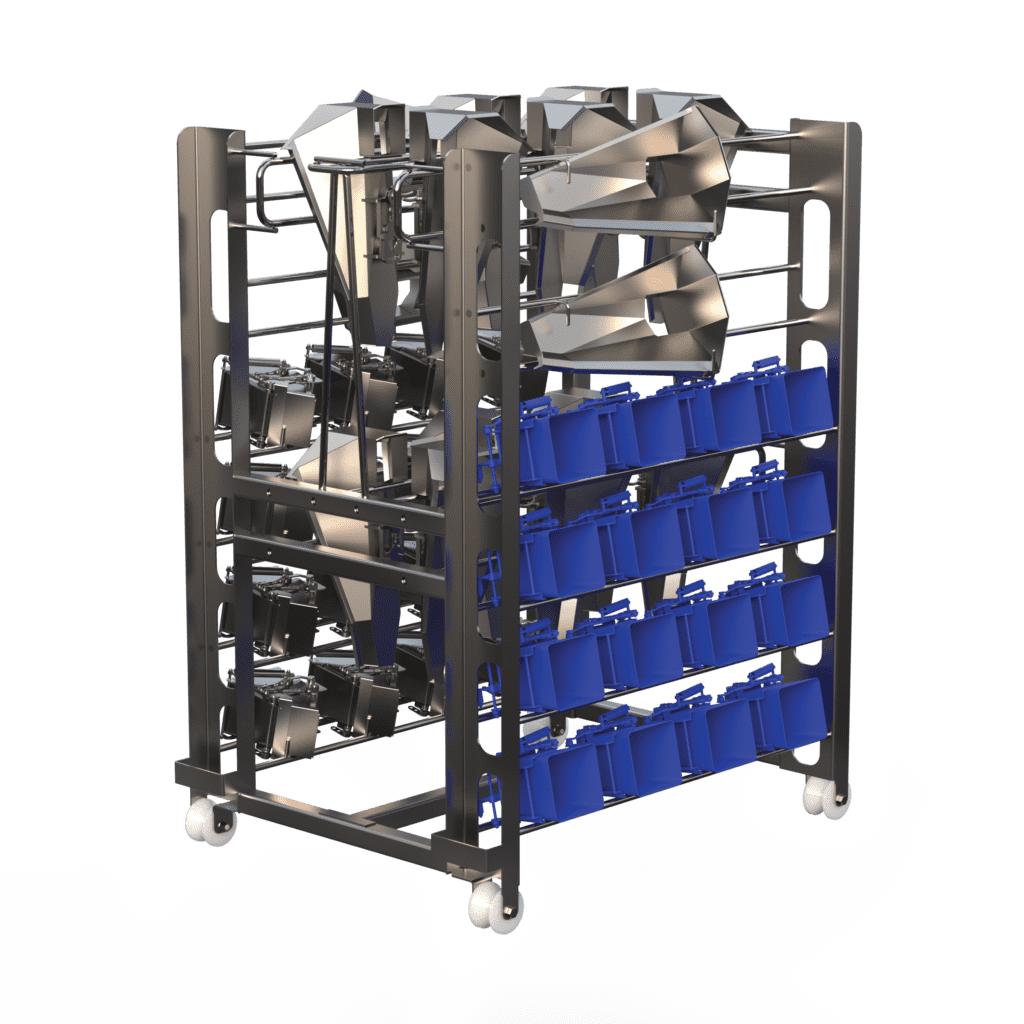
Improving Operator Safety
Cleaning processes can contain many hazards that an operator is exposed to. Some of the highest risk conditions include a combination of hot water, high pressure water, and cleaning chemicals. When manually cleaning, these conditions are open and exposed and in close contact to an operator.
Inherent to Cabinet Washers design is a cabinet, which has the part or parts inside of an enclosed area, so that all these conditions (heat, pressure, chemicals) are contained within the cabinet itself. This keeps the operator safe and away from these risks.
Data Recording
With the introduction of the Food Safety Modernization Act (FSMA) and most food processing facilities having implemented Hazard Analysis Critical Control Point (HACCP) plans, facilities know that keeping complete and thorough records of what goes on within the food processing plant is of utmost importance.
These record keeping requirements should and can be extended to cleaning record requirements. When it comes to manual cleaning, maintaining these records can be tough. Data recording relies on operators checking gauges for temperature or perhaps using titration strips for chemical concentration. Again, this is labor intensive and creates chances for errors or incomplete data.
Cabinet Washers automated PLC control allows for recording all critical cleaning cycle data through exporting the data from the wash cycle to software reporting packages external to the cleaning system. This allows for throughout and user-friendly cleaning cycle reports for each cleaning cycle that the cabinet washer runs.
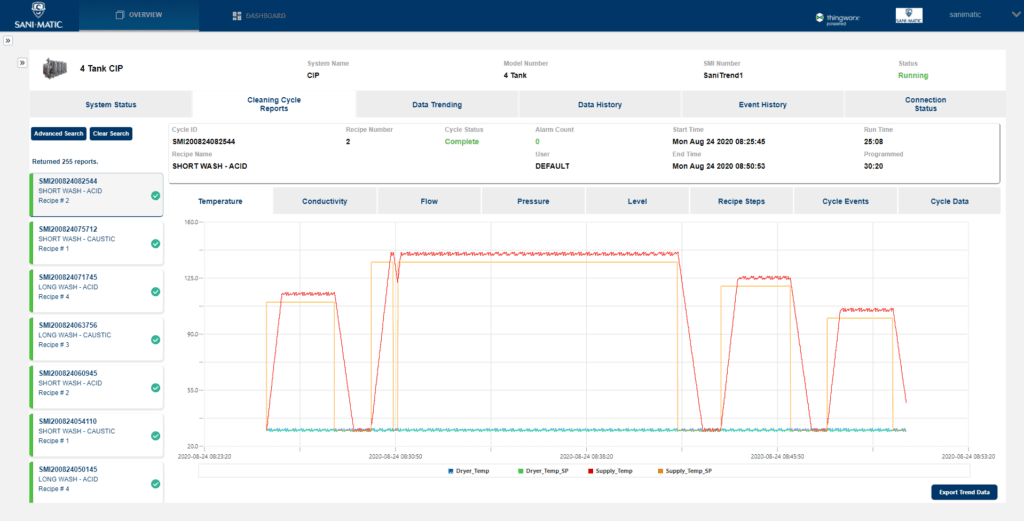
Automate Your COP Cleaning
The benefits of a Cabinet Washer type system for cleaning process parts out of place are clear. While more expensive than a traditional COP Parts Washer, virtually all facilities can outline a clear path to a quick return on investment. Often the two factors contributing the most to this quick return on investment are a reduction in labor and the quicker return to production (i.e., more production time!). Automate your COP cleaning today with a Cabinet Washer solution to see the benefits of this often overlooked solution.