Sani-Matic Services
Sani-Matic Services
Your Trusted Cleaning Partners from Purchase to Production
From process lines to tanks to any other type of part that needs to be cleaned, it is imperative that you are cleaning processes are effective and repeatable in order to protect your product, brand, and the end user.
Since 1946, Sani-Matic has been a trusted name in the industry, providing world class quality products and unparalleled expertise. Our knowledgeable staff is here to support you and your application no matter what. From our dedicated sales and application engineers available to advise and guide you on the proper solution to our experienced service team that will go the extra mile to ensure your system is right – Sani-Matic is here to help.
Explore
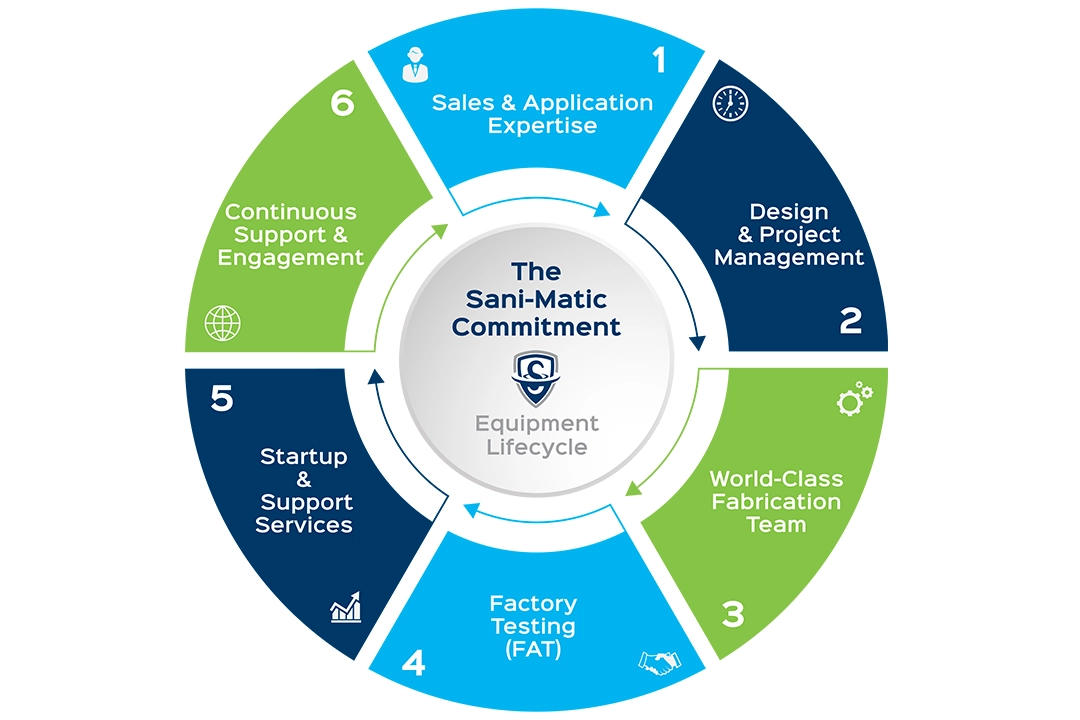
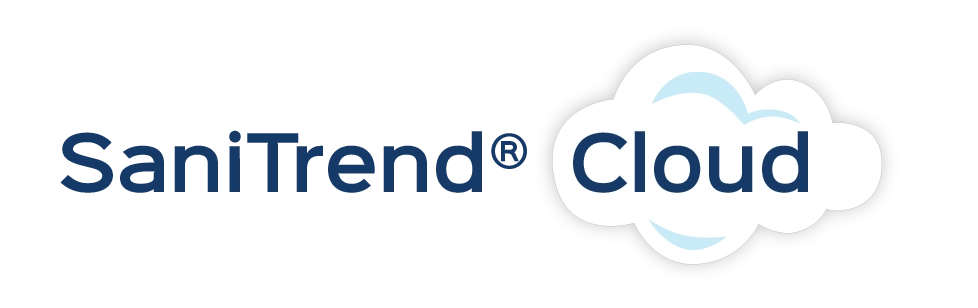
Automated Electronic CIP/COP
Data Recording, OEE, & More
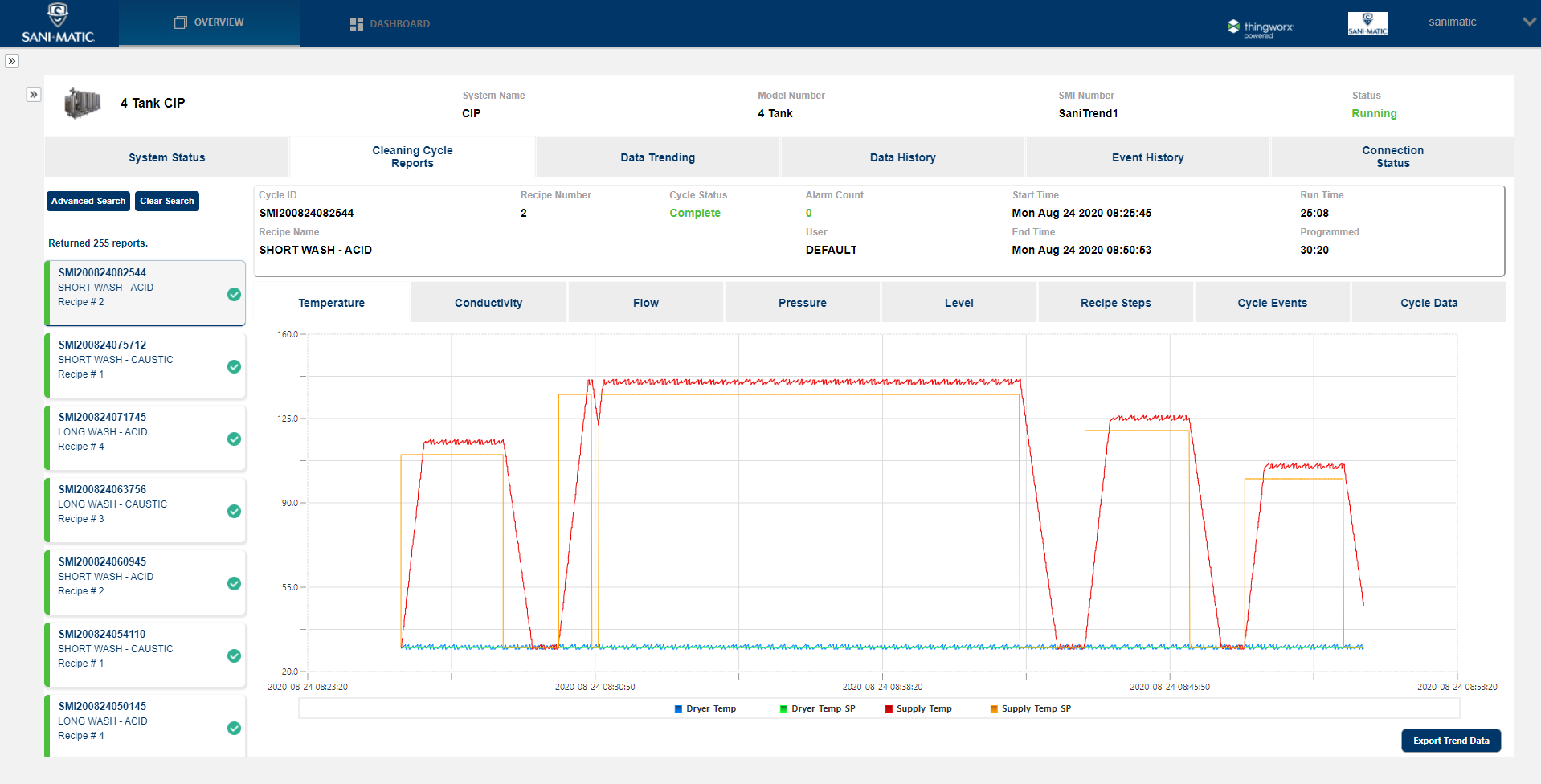
Sales & Application Expertise
Consulting & Expertise
Every facility has its own set of cleaning processes. These processes can change due to changing standards, new product introductions, or from a desire to improve efficiencies. Whether you are in the beginning stages of understanding what is important to you in your new cleaning process or in the middle of implementing your current plans, Sani-Matic has a dedicated team of sales and application engineers to help.
Contact us today to for a more in depth and detailed discussion of what solutions Sani-Matic can provide or to schedule an on-site audit cleaning and sanitation assessment today to have our world class evaluators evaluate your system.
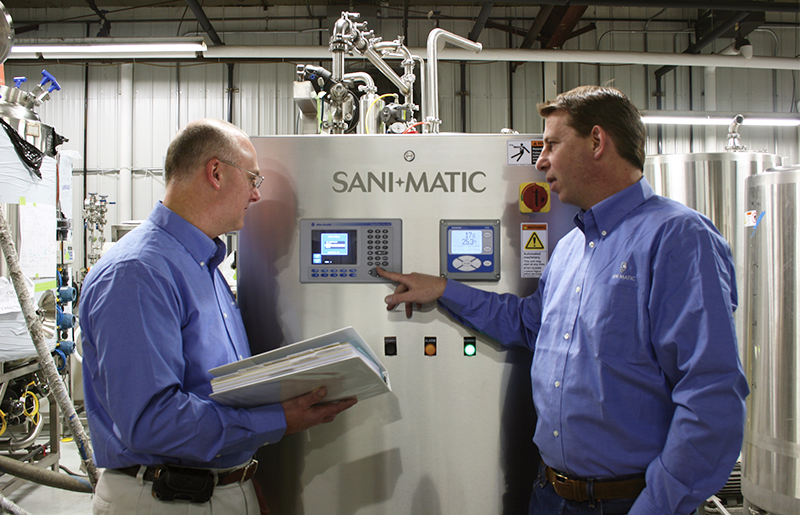
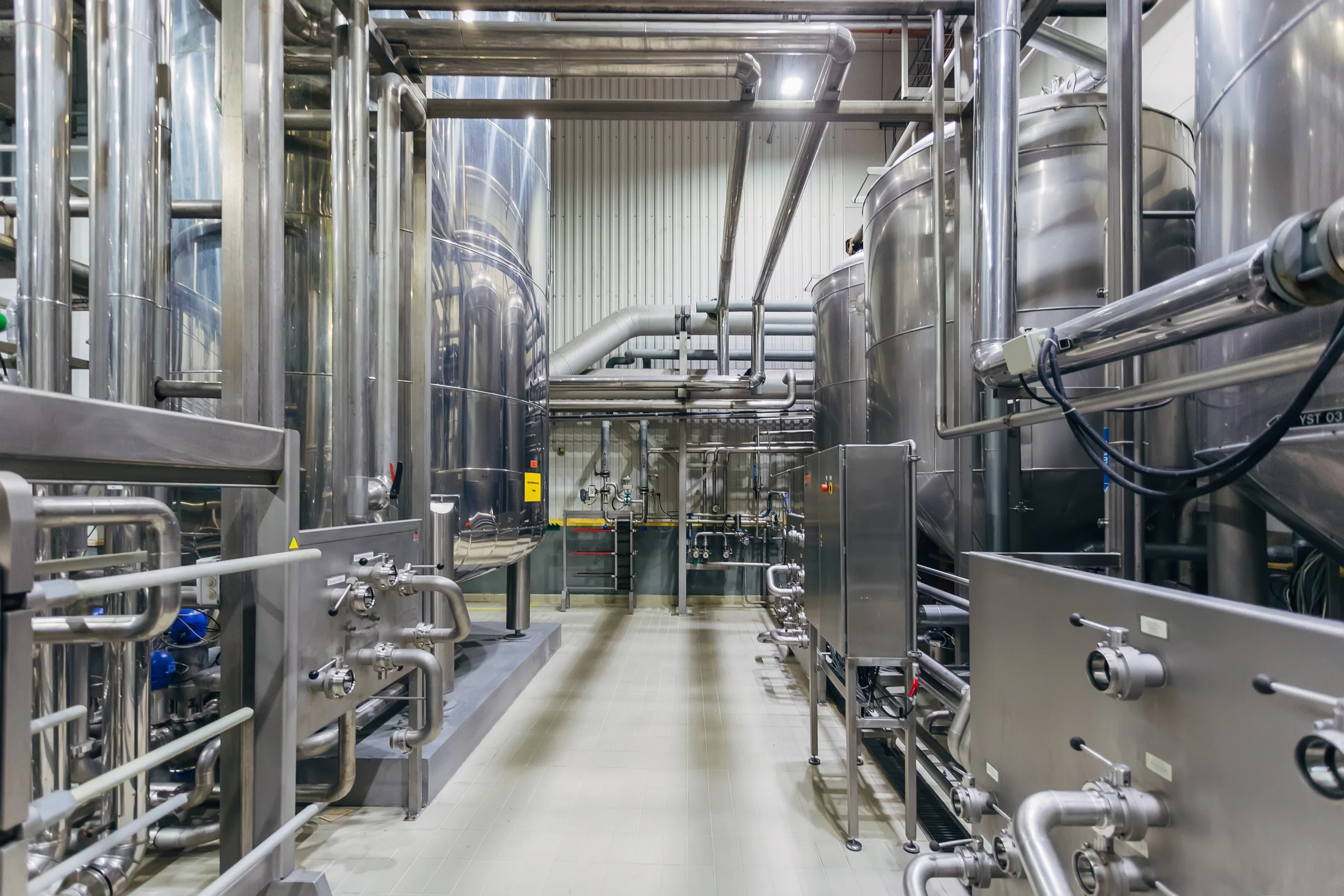
Cleaning & Sanitation Assessment
○ Does your cleaning process take long than it did at start-up?
○ Are you using more chemicals, water, or other utilities than desired?
○ Are your bacterial or ATP levels testing high?
No matter what your cleaning predicament is, Sani-Matic’s experienced team is available to visit your facility to speak with your operators, review standard sanitation operating procedures (SSOP’s), training protocols, process lines, equipment set points, operating recipes, and more.
The information from this assessment is aggregated in a detailed report proposing the necessary steps to address your challenges, optimize your system, promote worker safety and generate financial savings through efficiency gains.
Part Cleanability Evaluations
Every application is unique – from the soils and processes to the equipment and tools used. When considering if your application is right for a Clean-Out-of-Place (COP) equipment, Sani-Matic can facilitate a Part Cleaning Evaluation at our manufacturing facility in Sun Prairie, WI to ensure your parts can be cleaned to your standards.
Similar to our Site Cleaning Evaluations, Sani-Matic’s experienced team will work with you to understand the parts that need to be cleaned and discuss what results are important to your process.
We offer and recommend you attend the cleaning event, but if that isn’t an option, we will provide a detailed report with pictures highlighting how well we can clean your parts as well as provide recommendations on water and chemical usage, temperature requirements, and estimated cycle times.
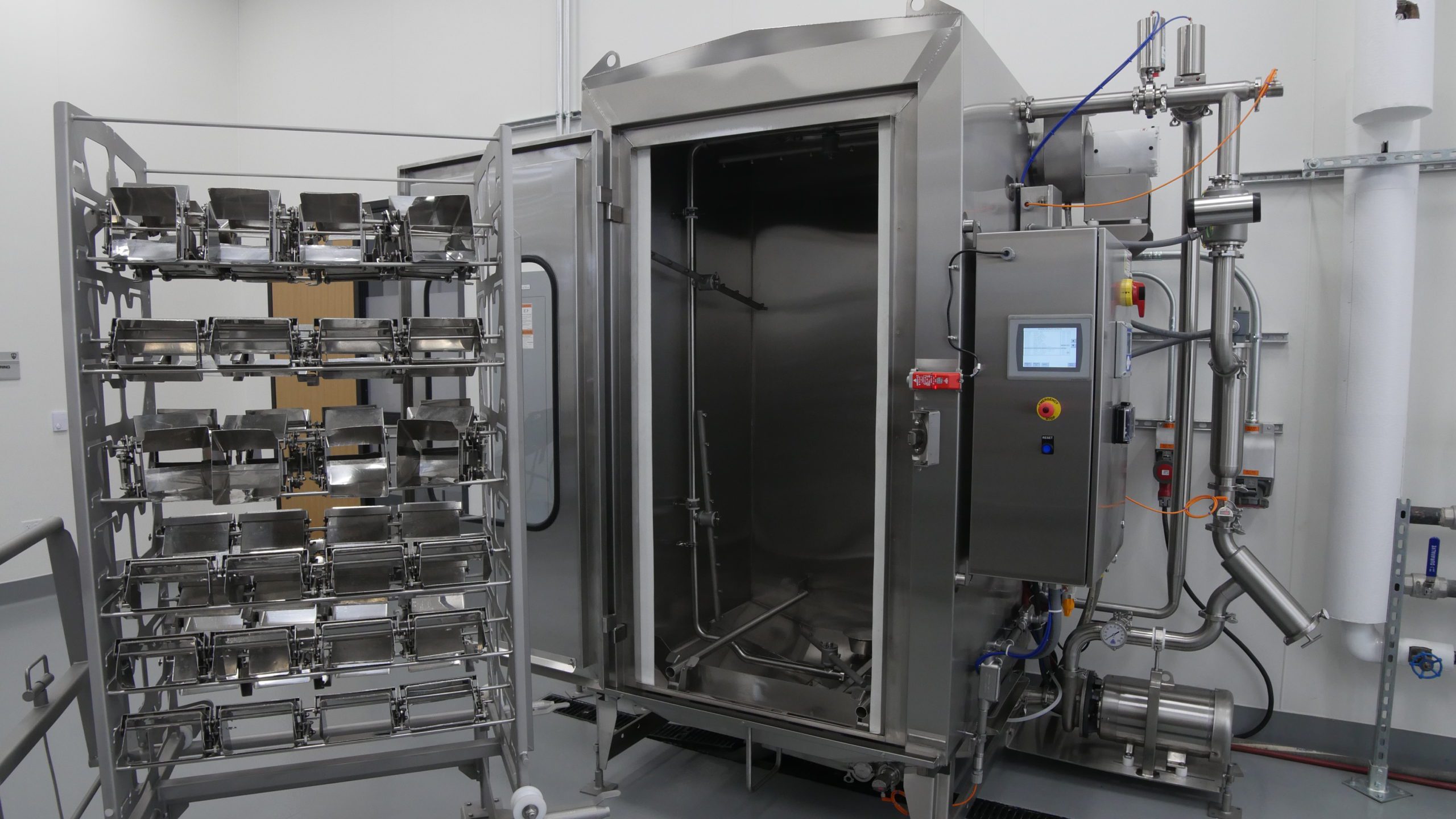
Start-up & Field Support
Ensure your Startup Goes Smoothly
You’ve worked with Sani-Matic from equipment design to factory acceptance test. Now you’re ready to put your sanitary process cleaning equipment to work.
Sani-Matic’s field service engineers are available to ensure your equipment is setup to operate as safely and efficiently as it was designed to do. Our Startup Services plans can include any of the following:
○ Installation Assistance
○ Site Acceptance Testing
○ Installation/Operation Qualification (IQ/OQ) Execution
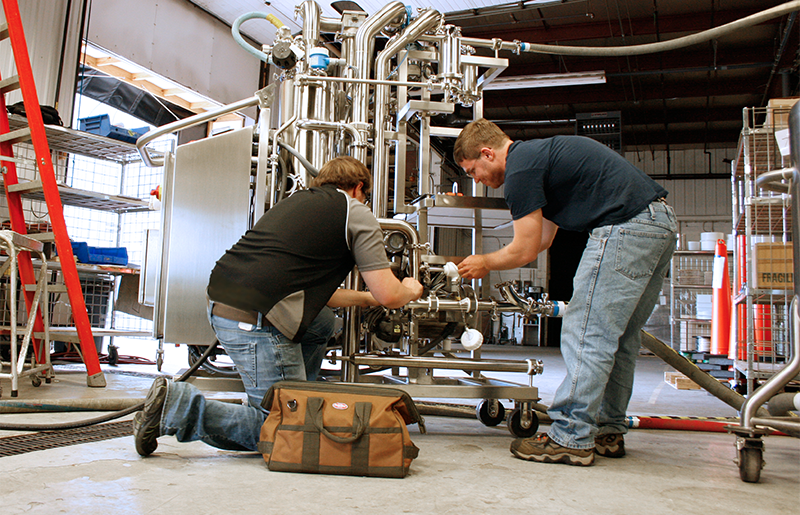
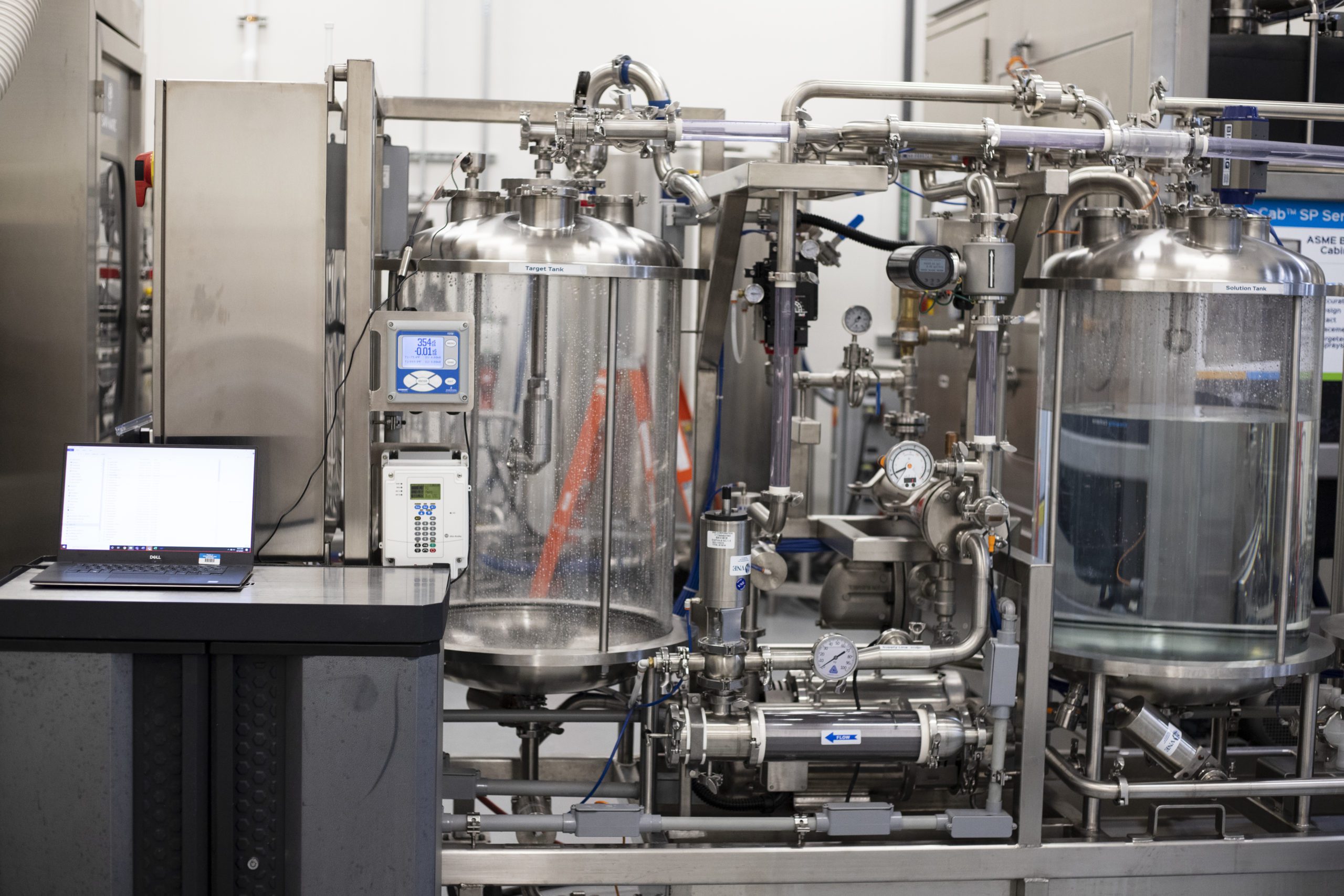
Field Support to Optimize, Troubleshoot, or Re-train your Staff
Processes and applications are always growing and evolving. Whether you’ve introduced a new product and are experiencing difficulties or have a need to re-train your staff, Sani-Matic can help.
Our Field Services team members have decades of experience installing systems, retrofitting equipment to accommodate process growth and changing needs, and refurbishing equipment to refresh it after years of hard use.
Continuous Support & Engagement
Follow-ups & Preventive Maintenance
After receiving, installing, and starting your new Sani-Matic equipment, over the course of the next months, we at Sani-Matic want to make sure your equipment is still running as expected. In the months following the integration of your equipment into your new processes, you can expect to have a representative from Sani-Matic following up to ensure we’ve met your expectation and discuss any of the following:
○ Discuss any questions or concerns
○ Preventative Maintenance (PM) Plans
○ On-Site Check-ins
○ Remote Troubleshooting Assistance
○ Stay up-to-date: newsletters, website content, & new product solutions
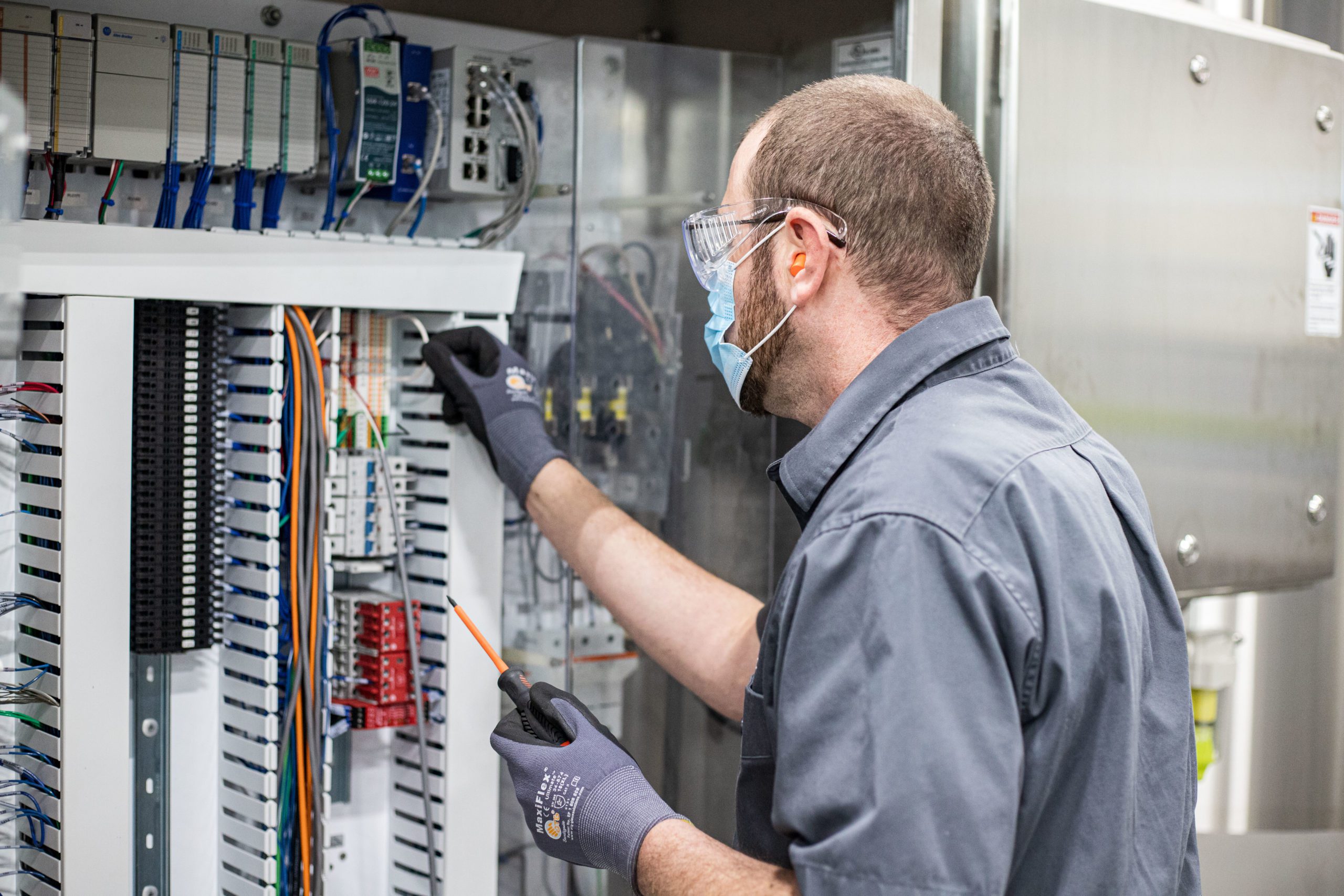
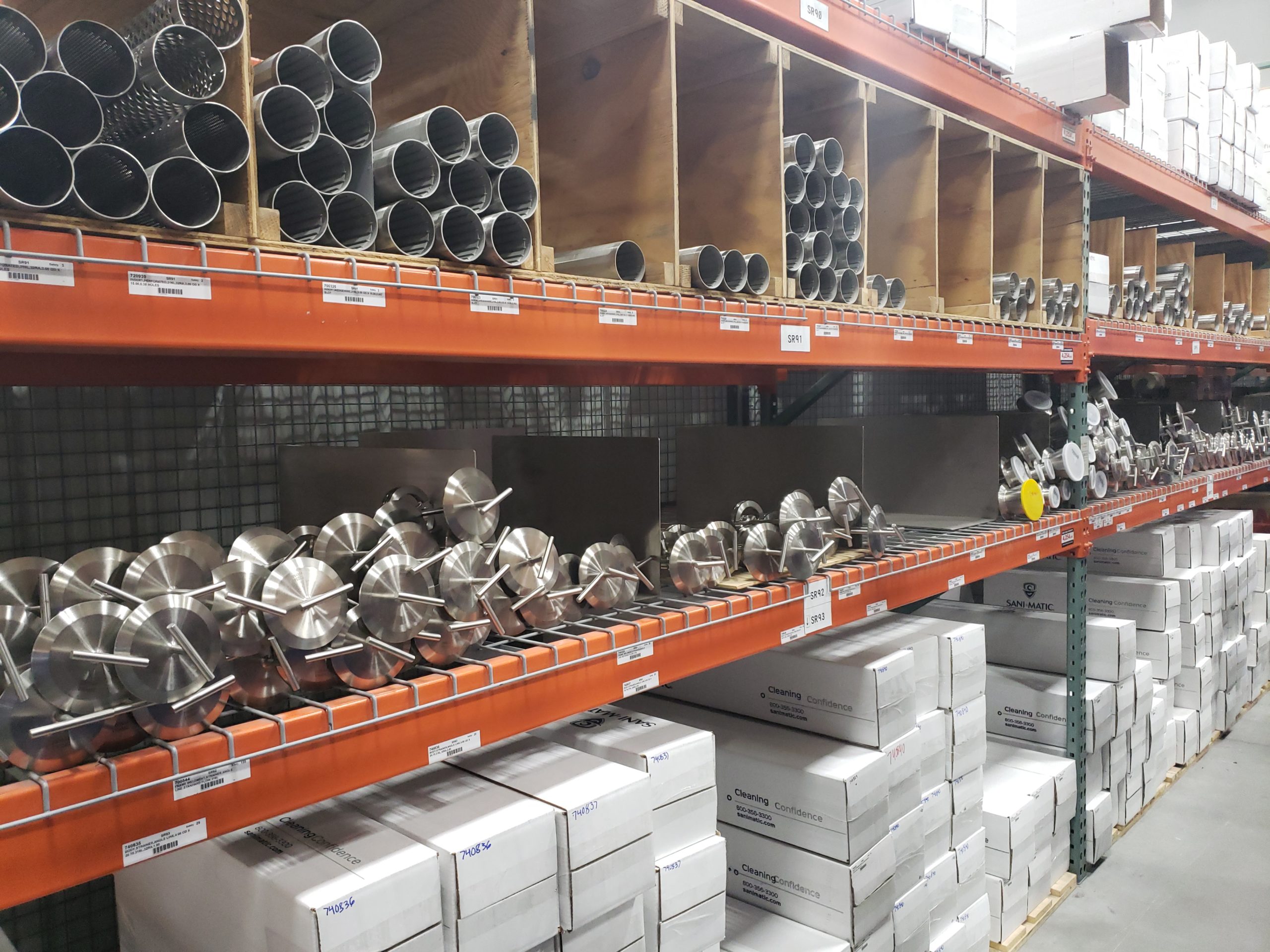
Process, Tank, & Replacement Parts
Sani-Matic stocks a large variety of components in our state-of-the-art manufacturing facility in Sun Prairie, WI, allowing us to provide you with the solution you need, when you need it.
Our Sanitary Components Catalog is a great starting point for both new and replacement components. We offer a wide variety of components from strainers and spray devices, to tank components, wash down equipment, and a wide variety of accessories.
Don’t see what you are looking for? Contact us today to get a quote!