Sanitary Dryer L
and L-HP
Standard Dry-In-Place (DIP) skidded system.
Dry sanitary process lines & small equipment.
Integrate with automated CIP or use standalone.
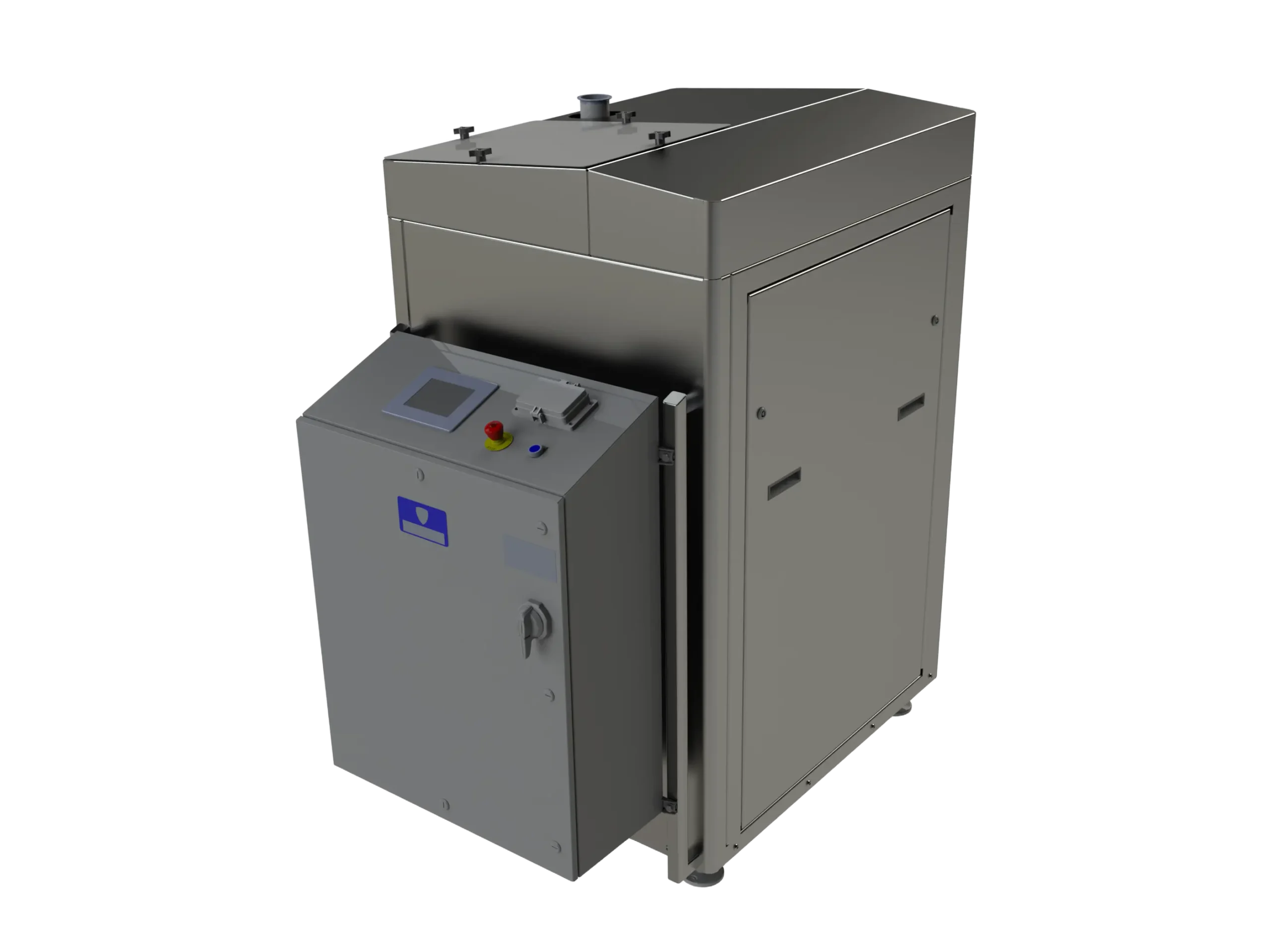
Sanitary Dryer L and L-HP
Automate Your Sanitary Drying Processes
Clean-In-Place (CIP) is a common method to automate the cleaning and sanitization of process lines – but if your process requires drying process lines or small equipment after CIP, it may still be a manual process.
Sani-Matic’s Sanitary Dryer L and L-HP automates this process to make drying as simple as the cleaning process.
Offered in 3 sizes for lines from 1.0″ to 4.0″, the Sanitary Dryer L system takes surrounding air and pre-filters it, delivering it to a regenerative blower controlled via VFD for adjustable setpoints. An electric heater and temperature
sensors help to monitor and control air temperature. Pressure and flow rate sensors allow for monitoring of these variables by the system.
The L-HP model adds HEPA level filtration for high purity applications in industries including personal care, nutraceutical, and bio-pharm, or where a higher filtration level of air drying is required.
SaniTrend ® Cloud or SaniTrend Local software packages are available as options, which enables fully automated reporting functionality, helping to meet FSMA reporting requirements for recording. SaniTrend Cloud’s online functionality also offers additional system insights including Overall Equipment Effectiveness (OEE) trending, live dashboards, preventive maintenance trackers, event notifications, and more.
Resources
View brochures, manuals, technical datasheets, or watch videos for this product.
Articles
Read articles written by industry leaders to share their expertise and recommendations.
Product Details
Sanitary Dryer L Models
L150
L300
L400
Applications (Process Lines – Sanitary Tube Sizes)
1.0″ – 1.5″
2.0″ – 3.0″
3.0″ – 4.0″
Example
Operating
Conditions
60 CFM @
300″ W.C.
200 CFM @
150″ W.C.
350CFM @
80″ W.C.
The HP line of the Sanitary Dryer adds additional filtration through use of a HEPA filter, while maintaining the above specifications.
Controls & Integration Options
CIP System Integration Controls
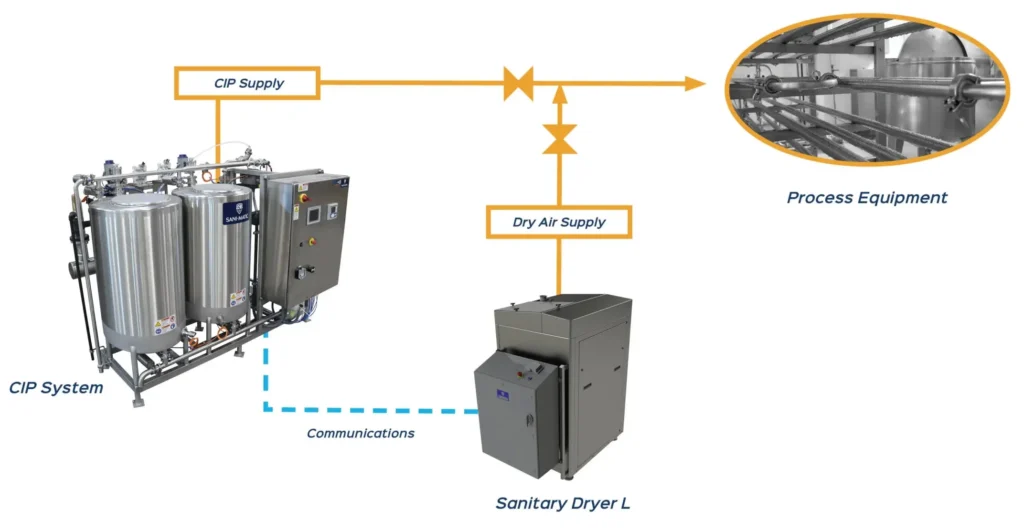
Stand-Alone Controls
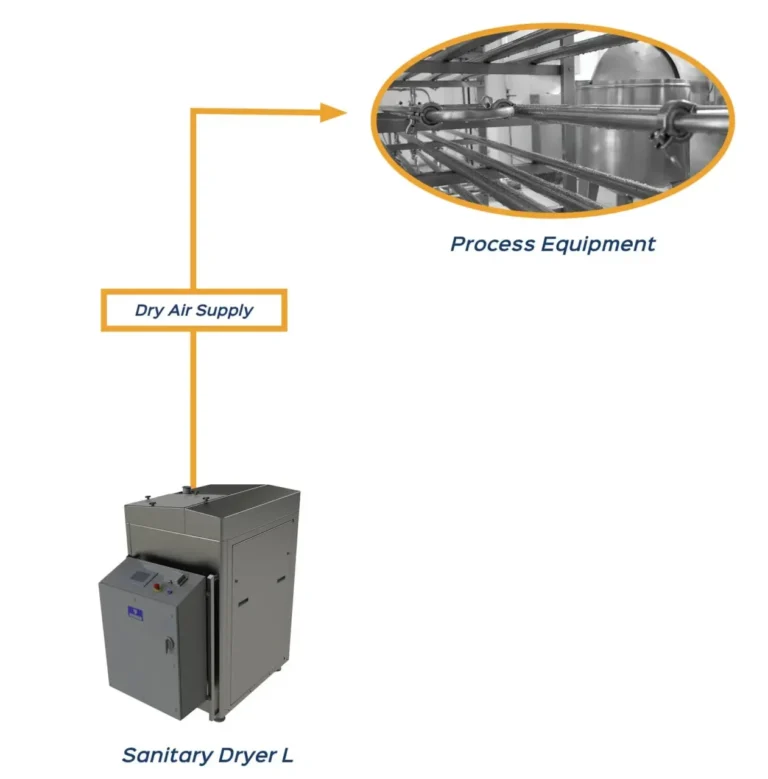