Tunnel
Washers
Effective Cleaning Systems for
High-Volume Processes

Tunnel Washers
Effective Cleaning Systems for High-Volume Processes
The automated Sani-Matic Tunnel Wash is designed to thoroughly clean large quantities of process items such as pans, totes or trays, while also generating labor, water, and chemical savings.
Each Tunnel Wash system has high-impact, 360° adjustable spray nozzle manifolds positioned to provide complete cleaning coverage of the process item’s internal and external surface area. The automated system has programmable controls to automate water levels, temperature and conveyor speeds for efficient, repeatable results and cost savings.
The basic Sani-Matic Tunnel Wash modular zone configuration includes detergent and final rinse zones. The most common layout, however, is a three-section tunnel wash that includes a detergent wash, recirculated rinse and final rinse.
If you have a lot of similar process items to clean in a short amount of time, a Tunnel Wash may be the ideal system to increase your productivity, decrease your costs and provide you with Cleaning Confidence.
Literature
View & download our latest manuals, technical datasheets, catalogs & more.
Articles
Read articles written by industry leaders to share their expertise and recommendations.
Product Resources
Literature
Videos
Product Details
Standard Features
○ 2-, 3- or 4-section modular configurations
○ 304ss construction
○ Rollaway covers for easy access to sprays, instruments and conveyor
○ Variable-speed, gear-driven conveyor with torque limiter
○ High-impact, 360° adjustable spray nozzle manifolds
○ Two-stage, solution straining system for heavy soil capture in the sump and fine particulate capture in the pump discharge
○ Pre-piped centrifugal supply pump(s)
○ Automatic temperature and water level controls with alarm and shutdown
○ Direct steam injection heating system
○ PLC Controls with control interface and indicator lights
○ Custom spray manifold/nozzle configuration
○ Custom guide rail container restraint system
○ Automatic final rinse control
How it Works
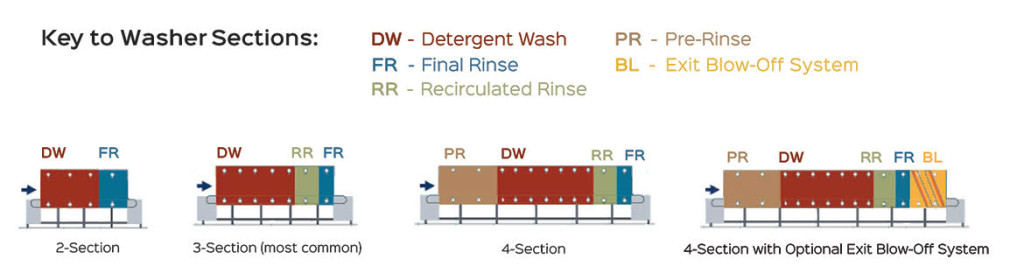
Operational overview of 4-section washer with exit blow-off system:
○ Soiled product containers are conveyed through the Pre-Rinse (PR) section to loosen and remove heavy residues.
○ The Detergent Wash (DW) section loosens and sprays off the remaining residue.
○ The Recirculated Rinse (RR) removes most of the residual detergent solutions from the containers and overflows to Pre-Rinse, if available.
○ The Fresh Water Rinse (FR) removes the remaining detergent film and overflows to Recirculated Rinse (RR).
○ Optional Exit Blow-Off System (BL).
Custom Options
○ Automatic detergent injections and concentration control
○ Automatic sanitizer injection system
○ Exit end blow-off system
○ PLC controls and plant control interface
○ Indirect steam heating coils
○ Conveyorized strainer with scraper
○ Final rinse conservation valve assembly
○ Exhaust fan
○ Single or dual lane configuration
○ Automated material handling capabilities
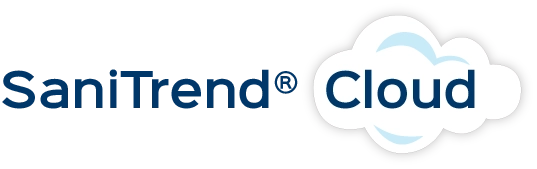
Automated Electronic CIP/COP
Data Recording, OEE, & More
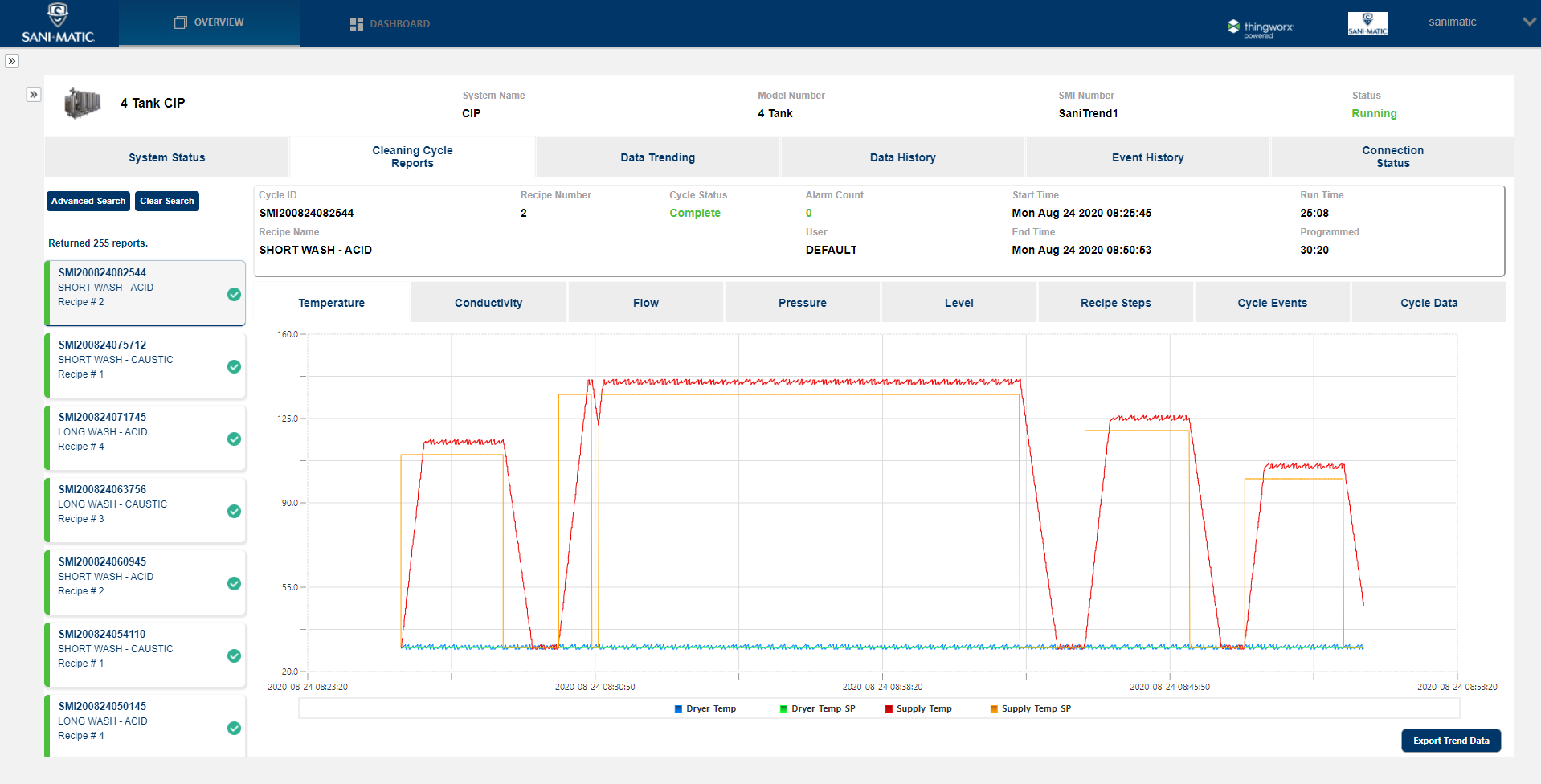